Recycled cordierite from EoL auto catalytic converters as feedstock for 3D printing
The ceramic substrate used in most catalytic converters (both its composition and architecture) was invented in the 1970s at Corning Inc. laboratories by Rodney Bagley, Irwin Lachman and Ronald Lewis, breakthrough which included them in the US National Inventors Hall of Fame in 2002. Their goal was to develop a highly refractory material with a minimum coefficient of thermal expansion (CTE), since it would be subjected to huge temperature variations. Additionally, the geometry should be designed to maximise surface exposure and optimise gas flow.
A synthetic version of the cordierite mineral, with composition Mg2Al4Si5O18, resulted to meet all the required properties (very low CTE, low thermal conductivity, wear and corrosion resistance…). Moreover, it could be easily produced from a mixture of inexpensive raw materials (alumina, talc, clay and silica), extruded into the desired hollow shapes, cut to length and calcined above 1400 °C [1].
Most catalytic converters nowadays are composed of a cordierite monolith with a thin-walled cell structure, acting as a support for the catalyst washcoat, a porous, thin layer (30-50 um) coating the ceramic substrate. The washcoat serves as a dispersion matrix for the precious metal (PM) catalysts (Pt, Pd, Rh) and is composed of a combination of refractory oxides (Al2O3, TiO2, SiO2, ZrO2, CeO2). Exhaust fumes from fuel combustion enter the catalytic converter where highly polluting gases are converted into less harmful ones. In particular, NOx are reduced to N2, while CO and hydrocarbons are oxidized to CO2 and water, with conversion efficiencies reported to be about 99% when new, and to taper off to 95% after about 6500 km.
In the PEACOC project, spent autocatalysts after pre-treatment and concentration stage, are subjected to MW-assisted leaching, a process that allows extracting PMs in solution, consuming significantly less energy with respect to current smelting processes (singnificantly reduced temperature and operation time). These solutions are further treated with the gas-diffusion electrocrystallisation (GDEx) technology, and PMs are efficiently recovered in metallic form.
But what about the solid residues? One of the goals of the PEACOC project is to recover and valorise them as well! In particular, the recycling strategy that has been identified for these mixtures of cordierite and low amounts of other oxides is their use as feedstock for the 3D printing of ceramic parts.
Preliminary trials by MBN Nanomaterialia (Italy), to upcycle these ceramic powders and evaluate their sinterability, have given promising results. In collaboration with 3DHub (Greece), efforts are now devoted to evaluating the most suitable 3d printing technique, i.e. paste extrusion, binder jetting, laser sintering, and to identifying the optimum process conditions.
Ideally, recycled cordierite from EoL catalyst converters after PMs recovery could be 3D printed into a novel catalyst converter, enabling the design of complex 3D channel architectures, not achievable by the current extrusion process. In this way, the exposed surface area could be considerably enhanced and the exhaust gas flow further optimised, to target even higher conversion efficiency of harmful pollutants [2].
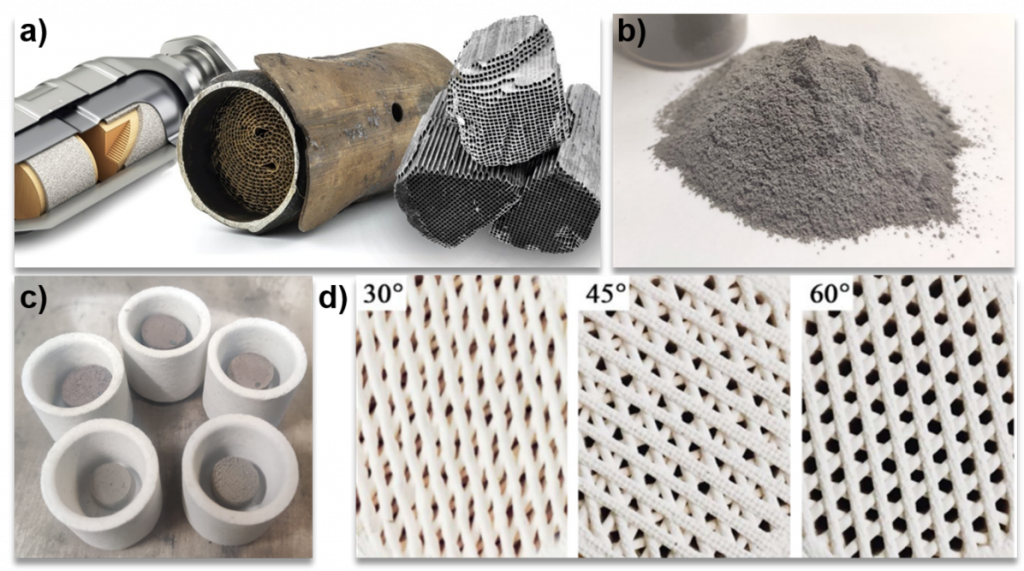
a) Spent auto catalytic converters, showing the honeycomb-shaped ceramic material inside. Image credit: Thermo Fischer Scientific. b) Spent auto catalyst after MW-leaching process, from VITO. c) Sintering trials of the powder in (b), from MBN Nanomaterialia. d) Example of 3d printed cordierite substrates with different channel geometries [2]
[1] Bagley, R. D.; Lachman, I. M.; Lewis, R. M. Extruded cordierite substrates for automotive emissions control. in Role of ceramics in a self-sustaining environment, edited by Pampuch, R.; Haberto, K., 37-68, Faenza, Techna, 1997.
[2] Hajimirzaee, S.; Doyle, A. M. 3D printed catalytic converters with enhanced activity for low-temperature methane oxidation in dual-fuel engines, Fuel, 2020, 274, 117848, https://doi.org/10.1016/j.fuel.2020.117848.