Optimisation and upscaling of the concentration stage – Retrieving value from old electronic devices
The exponential growth in the use of electronic devices and increasing consumerism has led to a major e-waste problem. Besides the risks raised by their incorrect disposal that could lead to hazardous materials leaching into the environment and harming human health and ecosystems, many electronic devices also contain valuable and scarce metals. Recovering and recycling these strategic materials has recently become as important as mining them, with the recently adopted Critical Raw Materials Act increasing the benchmark for EU recycling capacity of strategic raw materials to 25% of annual consumption by 2030.
Two of the innovative separation technologies have been developed and refined under the PEACOC project to optimise the recovery of precious metals (PMs). These innovations, known as NOVA [developed by the GeMMe Research Group at University of Liege (ULiège) (BE)], respectively the Magnetic Density Separation (MDS) [developed within the Faculty of Civil Engineering and Geosciences at University of Delft (TUD) (NED)], are now advancing to the upscaling phase, promising improvements in e-waste processing.
NOVA technology by GeMME Research Group at University of Liège
Research team at ULI received the prototype of the NOVA reactor, including drawings, inventories and the future design. The delivery of the NOVA prototype, designed to operate batches of 600 kg printed circuit board assemblies (PCBAs), is expected during the summer of 2024, which means the first batch of PM concentrates will be produced in the following month. During this waiting period, ULI members are already working on the logistics to accommodate the reception of the NOVA prototype in their premises.
Key features of NOVA
Using a combination of electrochemistry and mechanical activation, NOVA technology enables the detachment of electronic components soldered on the PCBA. Experimental work showed precious metals (PMs) can be concentrated mostly in the electronic components while few remain in the tin (Sn) concentrate and the copper-rich (Cu) depopulated PCBAs obtained from the NOVA process. These fractions can be further processed to valorise gold (Au) – from electronic components – and silver (Ag), Cu and Sn – from the Sn concentrate and depopulated PCBAs.
Magnetic Density Separation by TU Delft
On the other hand, at the Faculty of Civil Engineering and Geosciences, TU Delft, researchers have refined the MDS process. This technology uses a combination of roller sorting, a superconducting magnet, a magnetic fluid and a separation container precisely tailored after running various simulation models. The primary objective during the experimental activities aimed at consolidating the components containing Au, Ag and Pd with relatively high recoveries.
Upgrades in MDS
Compared with the initial tests, the preprocessing steps involving the roller sorter and ferromagnetic separator (and sieving) have been upgraded to improve the overall efficiency of the MDS process.
Simultaneously, the MDS process was upgraded with an inclined planar magnet working in tandem with a horizontal basin containing a magnetic static fluid as separation medium. The prototype has been currently tested to demonstrate continuous production and to reduce consumption of ferrofluid.
TUD has successfully submitted and approved three corresponding patents referring to the synthesis method of the ferrofluid used in this work, the design of the planar magnet and the design of the industrial facility based on innovative MDS process.
Commercialising economical separation technologies
At the end of 2023, the lab at TU Delft received an industrial MDS machine prototype, ‘courtesy’ of MYNE, a metal recycling company which recycles e-waste and cable harnesses – components otherwise exported outside of Europe for valorisation. The prototype, capable of processing 1.5 tonnes of e-waste per hour, features a conveyor belt, which facilitates continuous removal of the components.
Optimal flowsheet for e-waste processing
Based on the results reported until M36, researchers have identified the best concentration flowsheet for various end-of-life (EoL) PCBA grades, which combines the NOVA technology, TUD’s sorting technologies and the copper (Cu) leaching applied to electronic components smaller than 2 mm. This integrated approach is estimated to efficiently prepare PM concentrates from mid-grade PCBAs, such as the ones retrieved from LCD TVs, underlining economic and environmental benefits of advanced e-waste recycling technologies.
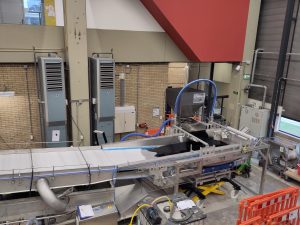
MDS prototype
©Photos: TU Delft and ULiège